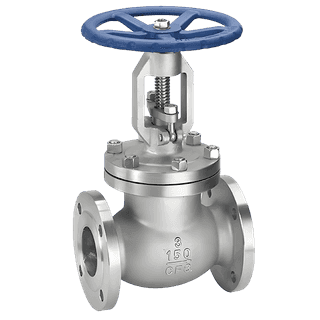
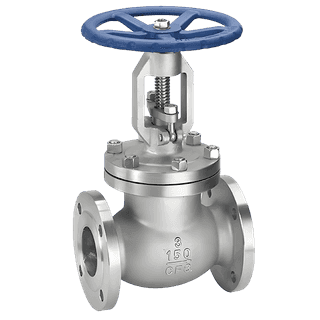
Globe Valve
In the realm of fluid control, the globe valve stands as a stalwart sentinel, its robust design and versatile functionality making it a cornerstone of various industrial applications. In this application introduction, we delve into the intricate details of the globe valve, exploring its structure, industrial implementations, usage instructions, failure analysis, and more.
Structure of Globe Valve
The globe valve derives its name from the globe-like shape of its body. It comprises several essential components, each playing a crucial role in its operation:
Body
The body of the globe valve serves as its primary housing, providing structural integrity and containment for the internal components.
Bonnet
Sitting atop the body, the bonnet encloses the valve's internal mechanism, safeguarding it from external elements.
Disc
Also known as the plug or disc, this component regulates the flow of fluid by moving against or away from the valve seat.
Valve Seat
The valve seat forms a tight seal with the disc, controlling the flow of fluid through the valve.
Stem
Connecting the actuator to the disc, the stem facilitates the movement of the disc within the valve body.
Actuator
In automated globe valves, the actuator serves as the driving force behind the movement of the disc, enabling precise control over fluid flow.
Industrial Applications
The versatility of the globe valve finds expression across a spectrum of industrial domains, owing to its robust construction and reliable performance. Some notable applications include:
Oil and Gas Industry
In the oil and gas sector, globe valves play a pivotal role in regulating the flow of crude oil, natural gas, and various petroleum by-products. From upstream extraction processes to downstream refining operations, these valves ensure efficient fluid control and safety.
Power Generation
Within power generation facilities, globe valves find application in steam systems, where they regulate the flow of high-pressure steam to turbines and other components. Their ability to withstand extreme temperatures and pressures makes them indispensable in maintaining operational efficiency and safety.
Chemical Processing
In chemical plants, where the handling of corrosive and hazardous fluids is commonplace, globe valves provide reliable fluid control and isolation. Their robust design and compatibility with a wide range of materials make them ideal for handling aggressive chemicals and maintaining process integrity.
Water Treatment
Municipal water treatment facilities rely on globe valves for regulating the flow of water through various treatment stages, including filtration, disinfection, and distribution. Their precise control capabilities ensure optimal performance and quality in water treatment processes.
HVAC Systems
In heating, ventilation, and air conditioning (HVAC) systems, globe valves are employed to modulate the flow of chilled water, hot water, and refrigerants, enabling precise temperature control and energy efficiency.
Case Study: Globe Valve in Petrochemical Refinery
To illustrate the practical significance of globe valves in industrial settings, let's consider a case study involving their use in a petrochemical refinery.
Scenario
In a petrochemical refinery, globe valves are deployed within the crude oil distillation unit to regulate the flow of various fractions during the refining process.
Application
Globe valves control the flow of crude oil feedstock, intermediate products, and refined fractions such as gasoline, diesel, and jet fuel. Their precise throttling action ensures optimal separation and purity of product streams, enhancing process efficiency and yield.
Benefits
- Reliable Operation: Globe valves withstand the harsh operating conditions prevalent in refinery environments, ensuring continuous and dependable performance.
- Process Flexibility: By adjusting the valve position, operators can fine-tune the flow rates of different fractions, accommodating variations in feedstock composition and process conditions.
- Safety Assurance: The tight shutoff capabilities of globe valves minimize the risk of leaks and spills, safeguarding personnel and equipment from potential hazards.
Usage Instructions
While globe valves offer exceptional performance and durability, proper usage and maintenance are essential to maximize their lifespan and efficiency. Here are some key instructions for operating and maintaining globe valves:
Installation
- Ensure proper alignment and support of the valve to prevent undue stress on the piping system.
- Tighten flange bolts uniformly to achieve a secure seal without distortion.
Operation
- Gradually open or close the valve to avoid sudden pressure surges that could damage the system.
- Periodically inspect the valve for signs of leakage or abnormal operation, such as excessive friction or sticking.
Maintenance
- Lubricate the valve stem and moving parts regularly to reduce friction and wear.
- Replace worn seals or gaskets promptly to prevent fluid leakage and ensure tight shutoff.
Failure Analysis
Despite their robust construction, globe valves may experience failures due to various factors, including:
Wear and Tear
Continuous operation under high-pressure conditions can lead to mechanical wear of valve components, such as the disc, seat, and stem.
Corrosion
Exposure to corrosive fluids or environments can degrade valve materials over time, leading to leakage or loss of sealing integrity.
Improper Maintenance
Neglecting routine lubrication, inspection, and maintenance can accelerate wear and compromise the performance of globe valves.
Operational Errors
Incorrect valve operation, such as rapid opening or closing, can induce stress on the valve mechanism, leading to mechanical failure or seal damage.
External Factors
External factors such as temperature fluctuations, vibration, and chemical exposure can impact the performance and longevity of globe valves.
Frequently Asked Questions (FAQs)
Q1: What distinguishes a globe valve from other types of valves?
A1: Unlike gate valves or ball valves, which offer full flow when fully open, globe valves provide precise throttling control over fluid flow due to their globe-shaped body and plug-like disc.
Q2: Can globe valves be used for both on-off and throttling applications?
A2: Yes, globe valves are versatile enough to perform both on-off and throttling functions, making them suitable for a wide range of industrial applications.
Q3: How do I determine the appropriate size of a globe valve for my application?
A3: The size of a globe valve is typically selected based on the desired flow rate, pressure drop, and pipe diameter of the system it will be installed in. Consulting with a qualified engineer or valve manufacturer can help determine the correct size for your specific application.
Q4: What maintenance tasks are required for globe valves?
A4: Routine maintenance tasks for globe valves include lubrication of moving parts, inspection for leaks or abnormal wear, and periodic replacement of seals or gaskets as needed.
Q5: Can globe valves be automated for remote operation?
A5: Yes, globe valves can be equipped with actuators and control systems to enable remote operation and integration into automated process control systems.
Conclusion
In conclusion, the globe valve emerges as a stalwart companion in the realm of fluid control, offering precision, reliability, and versatility across a myriad of industrial applications. From petrochemical refineries to water treatment plants, its robust construction and dependable performance make it an indispensable asset in ensuring operational efficiency and safety. By understanding its structure, applications, usage instructions, failure modes, and FAQs, engineers and operators can harness the full potential of the globe valve to meet their fluid control needs with confidence and efficacy.