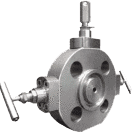
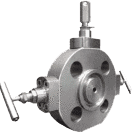
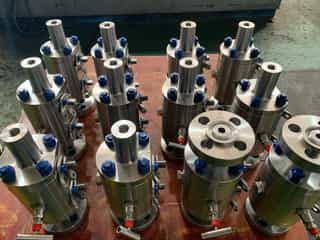
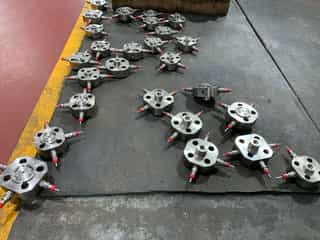
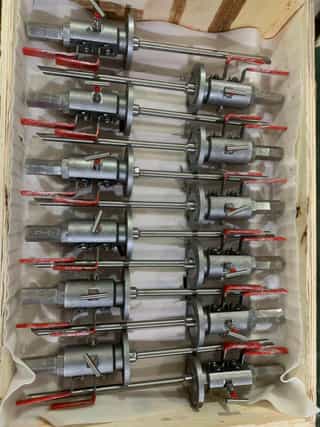
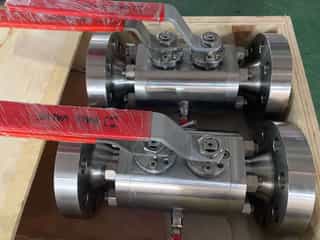
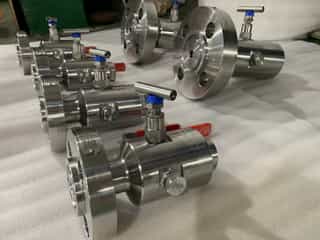
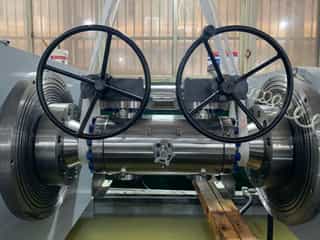
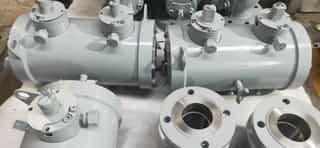
Double Block and Bleed Valve
In the realm of industrial valves, precision, reliability, and safety are paramount. One key innovation that has significantly enhanced these aspects is the Double Block and Bleed (DBB) valve. This ingenious engineering solution offers a robust mechanism for isolation and maintenance in various industrial applications. In this comprehensive guide, we delve into the structure, industrial applications, usage instructions, fault analysis, and FAQs surrounding the Double Block and Bleed Valve.
Understanding the Structure of Double Block and Bleed Valve
What is a Double Block and Bleed Valve?
Double Block and Bleed Valve is a sophisticated valve configuration consisting of two obturator seals and a vent valve, all integrated into a single valve body. This design enables the simultaneous isolation of both upstream and downstream flow, with a bleed valve for pressure relief or venting purposes.
Components of Double Block and Bleed Valve
- Dual Isolation Seals: These are the primary seals responsible for blocking the flow in both directions.
- Vent Valve: Positioned between the two isolation seals, the vent valve allows for pressure equalization or release.
- Valve Body: Houses all the components and provides the structural integrity required for high-pressure applications.
- Actuator: Depending on the application, manual, pneumatic, or hydraulic actuators can be integrated for valve operation.
Industrial Applications of Double Block and Bleed Valve
The versatility of Double Block and Bleed Valves makes them indispensable across various industries, including:
Oil and Gas Industry
In upstream, midstream, and downstream operations, DBB valves play a crucial role in pipeline isolation, maintenance, and safety. They are used in pigging, pressure monitoring, and sampling applications, ensuring the integrity and efficiency of oil and gas operations.
Petrochemical Industry
In petrochemical plants, where handling of volatile and hazardous fluids is routine, DBB valves provide essential safety measures. They enable safe isolation during maintenance activities, preventing the risk of leaks or spills that could lead to catastrophic incidents.
Chemical Processing
Chemical processing plants rely on DBB valves for precise control and isolation of fluids in various stages of production. From batch processing to reactor control, these valves ensure the integrity of processes while minimizing the risk of cross-contamination.
Power Generation
In power plants, where steam, water, and other fluids flow at high pressures and temperatures, DBB valves are deployed for isolation and safety. They facilitate maintenance shutdowns, emergency isolation, and flow diversion, enhancing the reliability of power generation systems.
Water and Wastewater Treatment
DBB valves find applications in water and wastewater treatment facilities for isolation and control of flow streams. They ensure the efficient operation of treatment processes while minimizing the risk of contamination or leakage.
Case Study: Utilizing Double Block and Bleed Valve in Offshore Oil Production
In a recent offshore oil production project, the implementation of Double Block and Bleed Valves proved instrumental in enhancing operational safety and efficiency. The project involved the installation of subsea pipelines for oil extraction, requiring robust isolation measures to maintain integrity and prevent environmental damage.
The DBB valves were strategically positioned along the pipeline route to allow for isolation during maintenance activities and emergency shutdowns. Their compact design and high-pressure rating made them ideal for subsea deployment, ensuring reliable performance in harsh offshore conditions.
During routine maintenance operations, the DBB valves facilitated quick and safe isolation of pipeline sections, minimizing production downtime and optimizing maintenance schedules. Furthermore, the integration of remote monitoring systems allowed for real-time valve status monitoring, enhancing operational visibility and control.
In the event of a pipeline leak or rupture, the DBB valves provided fail-safe isolation, preventing the spread of oil and minimizing environmental impact. This proactive approach to safety not only safeguarded the surrounding ecosystem but also mitigated potential liabilities for the operating company.
Usage Instructions for Double Block and Bleed Valve
Proper installation and operation of Double Block and Bleed Valves are essential for ensuring optimal performance and safety. Here are some key usage instructions:
- Pre-Installation Inspection: Before installation, inspect the valve body, seals, and actuator for any damage or defects. Ensure proper alignment and connection of piping.
- Valve Operation: Follow the manufacturer's guidelines for operating the valve, whether manual, pneumatic, or hydraulic. Exercise caution when actuating the valve to avoid damage to internal components.
- Pressure Relief: Use the vent valve to relieve pressure before performing maintenance activities or isolating the valve. Verify that the system is depressurized before proceeding.
- Maintenance Schedule: Establish a regular maintenance schedule for inspecting and servicing the valve components. Replace worn seals or damaged parts promptly to prevent leakage or failure.
- Emergency Procedures: Familiarize personnel with emergency procedures for isolating the valve in the event of a leak or rupture. Implement remote monitoring systems for real-time valve status updates.
Fault Analysis of Double Block and Bleed Valve
Despite their robust design and reliability, Double Block and Bleed Valves may experience faults or malfunctions under certain conditions. Here are some common fault scenarios and their analysis:
- Leakage: If the valve exhibits leakage, inspect the seals and valve body for damage or wear. Tighten connections and replace faulty seals to restore integrity.
- Actuator Failure: In case of actuator failure, check for hydraulic or pneumatic system malfunctions. Replace damaged actuators or repair the control system to restore functionality.
- Corrosion: Corrosion of valve components can lead to reduced performance and eventual failure. Implement corrosion prevention measures such as coatings or cathodic protection to prolong valve life.
- Blockage: Blockage of the valve internals can occur due to debris or sediment accumulation. Flush the valve system and inspect for obstructions, ensuring unobstructed flow.
- Seal Degradation: Over time, seals may degrade due to exposure to harsh operating conditions or chemical attack. Monitor seal condition regularly and replace as necessary to maintain sealing integrity.
Frequently Asked Questions (FAQs)
Q1: Can Double Block and Bleed Valves be used in high-pressure applications?
A1: Yes, Double Block and Bleed Valves are specifically designed to withstand high-pressure environments, making them suitable for a wide range of industrial applications.
Q2: How do Double Block and Bleed Valves differ from traditional isolation valves?
A2: Unlike traditional isolation valves, DBB valves feature two independent seals for double isolation, along with a vent valve for pressure relief or venting purposes, offering enhanced safety and reliability.
Q3: Are Double Block and Bleed Valves suitable for subsea applications?
A3: Yes, Double Block and Bleed Valves are commonly used in subsea oil and gas production due to their compact design, high-pressure rating, and reliability in offshore environments.
Q4: What maintenance procedures are required for Double Block and Bleed Valves?
A4: Regular inspection of seals, valve body, and actuators is essential to ensure proper functioning. Additionally, flushing the valve system and replacing worn components are recommended maintenance procedures.
Q5: How do I select the appropriate Double Block and Bleed Valve for my application?
A5: Consider factors such as operating pressure, temperature, fluid compatibility, and environmental conditions when selecting a DBB valve. Consult with valve manufacturers or industry experts for guidance on valve selection.
Conclusion
Double Block and Bleed Valves represent a pinnacle of engineering innovation, offering unparalleled safety, reliability, and performance in industrial applications. From oil and gas production to chemical processing, these valves play a crucial role in ensuring operational integrity and minimizing risks. By understanding their structure, applications, usage instructions, and fault analysis, industries can leverage the full potential of Double Block and Bleed Valves to enhance productivity and safety standards.