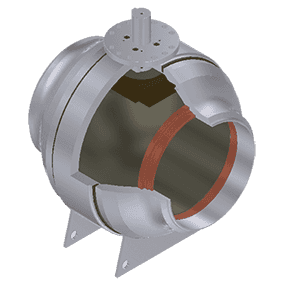
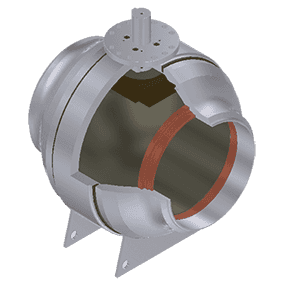
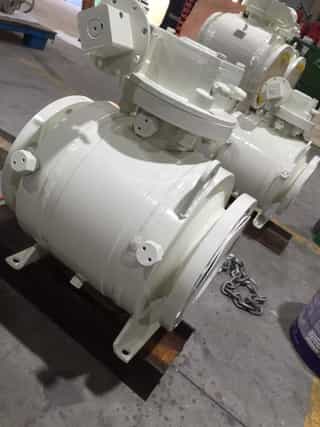
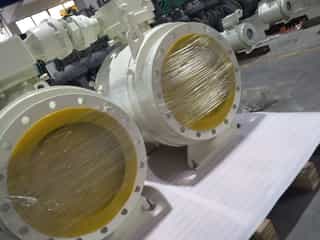
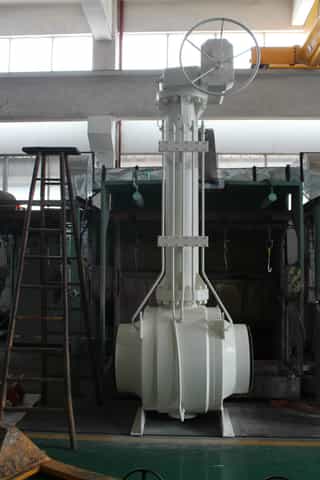
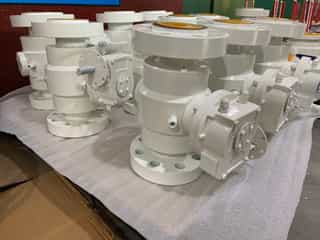
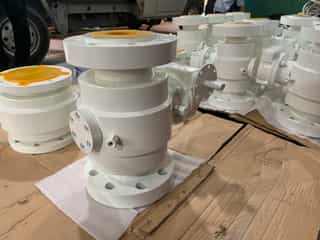
Full Welded Ball Valve
In the realm of industrial valves, the full welded ball valve stands out as a pinnacle of engineering excellence, combining robust construction with unparalleled safety features. In this comprehensive guide, we delve into the intricacies of full welded ball valves, exploring their structure, industrial applications, usage instructions, fault analysis, and more. Let's embark on a journey to uncover the essence of these indispensable components of fluid control systems.
Structure of Full Welded Ball Valve
A full welded ball valve comprises several essential components meticulously designed to ensure optimal performance and reliability. At its core lies a spherical ball with a central bore, which serves as the primary mechanism for regulating fluid flow. This ball is typically crafted from durable materials such as stainless steel or brass, ensuring longevity and resistance to corrosion.
Surrounding the ball, there are two or more seats, commonly made of resilient materials like PTFE (Polytetrafluoroethylene), ensuring a tight seal and preventing leakage. The valve body, usually constructed from carbon steel or stainless steel, provides structural integrity and houses the internal components securely. Additionally, full welded ball valves often feature actuation mechanisms, such as manual levers or pneumatic actuators, facilitating seamless operation.
Industrial Applications of Full Welded Ball Valves
Full welded ball valves find extensive utilization across a diverse range of industrial sectors, owing to their unparalleled reliability and safety features.
Oil and Gas Industry
In the oil and gas industry, where safety and efficiency are paramount, full welded ball valves play a crucial role in controlling the flow of various fluids, including crude oil, natural gas, and refined products. These valves are often employed in pipelines, refineries, and storage facilities, where they ensure smooth operation while minimizing the risk of leakage or spills.
Petrochemical Plants
Petrochemical plants rely on full welded ball valves to regulate the flow of aggressive chemicals and hazardous substances with precision and reliability. These valves offer exceptional chemical resistance and are capable of withstanding high temperatures and pressures, making them indispensable in chemical processing applications.
Power Generation
Full welded ball valves play a vital role in power generation plants, where they are utilized in steam systems, cooling circuits, and fuel handling processes. By providing reliable fluid control, these valves contribute to the efficient operation of power generation equipment while minimizing downtime and maintenance costs.
Case Study: Full Welded Ball Valve in Offshore Oil Rig
Consider a scenario where a full welded ball valve is installed in an offshore oil rig to regulate the flow of crude oil from subsea wells to the surface processing facilities.
Usage Instructions
- Installation: Ensure proper alignment and secure mounting of the valve to prevent misalignment or damage during operation.
- Operation: Use the designated actuation mechanism to open or close the valve smoothly, avoiding abrupt movements that may cause wear or damage.
- Maintenance: Regularly inspect the valve for signs of wear, corrosion, or leakage, and perform necessary maintenance tasks such as lubrication or replacement of seals.
- Safety Precautions: Adhere to all safety protocols and guidelines while operating the valve, including the use of personal protective equipment and isolation procedures.
Fault Analysis
In the event of a malfunction or fault in the full welded ball valve, a systematic analysis must be conducted to identify the root cause and implement appropriate corrective measures. Common issues include:
- Leakage: Inspect the valve seats and seals for damage or wear, and replace them if necessary to restore the integrity of the seal.
- Sticking: Check for debris or foreign objects obstructing the movement of the ball, and clean the internal components thoroughly to ensure smooth operation.
- Actuator Failure: Evaluate the condition of the actuation mechanism and address any mechanical or electrical faults to restore functionality.
- Corrosion: Examine the valve body and internal components for signs of corrosion, and implement corrosion prevention measures such as coatings or cathodic protection.
- Pressure Fluctuations: Analyze the system pressure and fluid dynamics to determine the cause of pressure fluctuations, and adjust the valve settings accordingly to maintain stable operation.
Frequently Asked Questions (FAQs)
1. Are full welded ball valves suitable for high-pressure applications?
Yes, full welded ball valves are designed to withstand high pressures and are commonly used in industries such as oil and gas, where operating conditions can be extremely demanding.
2. What are the advantages of full welded ball valves over traditional valve designs?
Full welded ball valves offer several advantages, including superior sealing performance, reduced risk of leakage, and enhanced durability due to their robust construction.
3. Can full welded ball valves be installed in underwater environments?
Yes, full welded ball valves are well-suited for subsea applications and are often used in offshore oil and gas production facilities to control the flow of fluids beneath the ocean surface.
4. How do I ensure the safety of full welded ball valve operation?
To ensure safe operation of full welded ball valves, follow all recommended usage instructions, conduct regular maintenance inspections, and adhere to relevant safety protocols and guidelines.
5. What factors should I consider when selecting a full welded ball valve for my application?
When selecting a full welded ball valve, consider factors such as the fluid properties, operating conditions (including temperature and pressure), environmental factors, and regulatory requirements to ensure compatibility and optimal performance.
Conclusion
In conclusion, full welded ball valves represent a pinnacle of engineering excellence, offering unmatched reliability, safety, and performance in fluid control applications across various industries. With their robust construction, precise operation, and exceptional sealing capabilities, these valves continue to play a vital role in ensuring the efficiency and safety of industrial processes worldwide. By understanding their structure, applications, and maintenance requirements, engineers and operators can harness the full potential of full welded ball valves to achieve optimal performance and mitigate operational risks effectively.