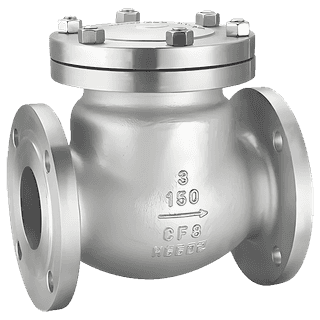
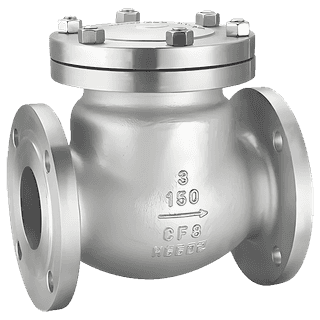
Swing Check Valve
In the realm of fluid control, the swing check valve stands as a stalwart sentinel, its robust design and versatile functionality making it a cornerstone of various industrial applications. In this application introduction, we delve into the intricate details of the swing check valve, exploring its structure, industrial implementations, usage instructions, failure analysis, and more.
Structure of Swing Check Valve
The swing check valve derives its name from the swinging motion of its disc to regulate fluid flow. It comprises several essential components, each playing a crucial role in its operation:
Body
Similar to other types of valves, the body of the swing check valve provides structural support and containment for the internal components.
Disc
The distinctive feature of the swing check valve is its hinged disc, which swings open and closed to allow or prevent the flow of fluid through the valve.
Seat
The valve seat forms a tight seal with the disc when closed, preventing backflow of fluid and ensuring system integrity.
Hinge Pin
Connecting the disc to the valve body, the hinge pin allows the disc to pivot freely, facilitating smooth operation.
Spring (Optional)
Some swing check valves incorporate a spring mechanism to assist in closing the disc quickly and efficiently, reducing the risk of reverse flow.
Industrial Applications
The versatility of the swing check valve makes it indispensable in various industrial sectors, where reliable fluid control is paramount. Let's explore some of its primary applications:
Water Distribution
In water distribution systems, swing check valves prevent backflow of water, ensuring the integrity of potable water supplies and preventing contamination.
Wastewater Treatment
Within wastewater treatment plants, swing check valves regulate the flow of sewage and effluent, preventing backflow and maintaining the efficiency of treatment processes.
HVAC Systems
Swing check valves play a crucial role in heating, ventilation, and air conditioning (HVAC) systems, where they prevent reverse flow of chilled water, hot water, or refrigerants, maintaining system efficiency.
Fire Protection
In fire protection systems, swing check valves ensure that water flows in only one direction, preventing backflow and ensuring the availability of water for firefighting purposes.
Industrial Processes
In various industrial processes such as chemical manufacturing, power generation, and petrochemical refining, swing check valves are used to control the flow of fluids and prevent backflow, safeguarding equipment and ensuring operational efficiency.
Case Study: Swing Check Valve in Water Distribution System
To illustrate the practical significance of swing check valves in real-world applications, let's consider a case study involving their use in a municipal water distribution system.
Scenario
In a municipal water distribution system, swing check valves are installed at strategic points along the pipeline network to prevent backflow and maintain system integrity.
Application
Swing check valves ensure that water flows in only one direction, preventing contamination of the potable water supply by backflow from consumer premises or industrial facilities.
Benefits
- Contamination Prevention: By effectively preventing backflow, swing check valves safeguard the quality and safety of the municipal water supply, minimizing the risk of waterborne diseases and contamination.
- System Integrity: The reliable performance of swing check valves helps maintain the hydraulic integrity of the water distribution system, ensuring consistent water pressure and flow rates to consumers.
- Regulatory Compliance: Compliance with regulatory standards for water quality and distribution is facilitated by the use of swing check valves, which help municipalities meet their legal obligations and ensure public health and safety.
Usage Instructions
While swing check valves are relatively simple in design, proper installation, operation, and maintenance are essential to their reliable performance. Here are some key instructions for using swing check valves effectively:
Installation
- Ensure proper alignment and orientation of the valve to facilitate optimal flow direction and prevent misalignment or binding.
- Securely anchor the valve to the pipeline to prevent movement or vibration during operation.
Operation
- Check the swing mechanism periodically to ensure smooth and unobstructed movement of the disc.
- Monitor valve performance for any signs of leakage, sticking, or abnormal operation, and address any issues promptly.
Maintenance
- Inspect the valve regularly for signs of corrosion, wear, or damage, and replace any worn or damaged components as needed.
- Lubricate moving parts, such as the hinge pin and disc pivot, to maintain smooth operation and prevent friction-induced wear.
Failure Analysis
Despite their robust construction, swing check valves may experience failures due to various factors, including:
Corrosion
Exposure to corrosive fluids or environments can degrade valve materials over time, leading to leakage or loss of sealing integrity.
Mechanical Wear
Continuous operation and cycling of the valve disc can result in mechanical wear of hinge pins, disc seats, and sealing surfaces, compromising performance.
Improper Installation
Incorrect installation or misalignment of swing check valves can lead to binding, sticking, or inadequate sealing, resulting in reduced efficiency and reliability.
Sediment Buildup
Accumulation of sediment or debris within the valve body can obstruct the movement of the disc and impede proper valve operation, leading to flow restriction or blockage.
Hydraulic Shock
Sudden changes in fluid flow velocity or pressure, known as hydraulic shock or water hammer, can exert excessive force on swing check valves, potentially causing damage to internal components.
Frequently Asked Questions (FAQs)
Q1: How does a swing check valve differ from other types of check valves?
A1: Unlike ball check valves or lift check valves, which rely on different mechanisms for fluid control, swing check valves utilize a hinged disc that swings open and closed to regulate flow.
Q2: Can swing check valves be installed in horizontal and vertical pipelines?
A2: Yes, swing check valves are versatile enough to be installed in both horizontal and vertical orientations, provided that proper support and alignment are ensured to facilitate optimal valve operation.
Q3: What factors should be considered when selecting a swing check valve for a specific application?
A3: Key factors to consider include flow rate, pressure rating, fluid compatibility, temperature range, and installation requirements, as well as regulatory compliance and industry standards.
Q4: Are swing check valves suitable for use with abrasive or slurry fluids?
A4: While swing check valves can handle a wide range of fluids, including slurries and abrasive media, special considerations may be necessary to mitigate wear and erosion of valve components in such applications.
Q5: Can swing check valves be repaired or refurbished if they develop leaks or mechanical issues?
A5: Depending on the extent of damage or wear, swing check valves may be repairable through replacement of worn components, refurbishment of sealing surfaces, or reconditioning of internal mechanisms.
Conclusion
In conclusion, the swing check valve emerges as a vital component in fluid control systems across various industrial sectors, offering reliability, versatility, and efficiency in regulating fluid flow and preventing backflow. Whether safeguarding municipal water supplies, enhancing process efficiency in industrial applications, or ensuring system integrity in HVAC and fire protection systems, swing check valves play a crucial role in maintaining operational reliability and safety. By understanding their structure, applications, usage instructions, failure modes, and FAQs, engineers and operators can effectively leverage the capabilities of swing check valves to meet their fluid control needs with confidence and efficacy.