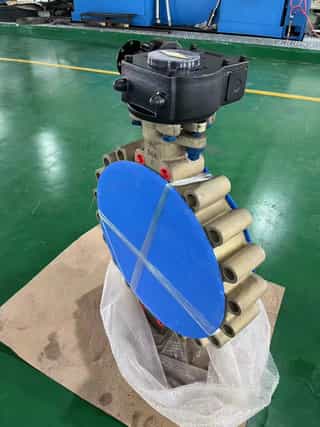
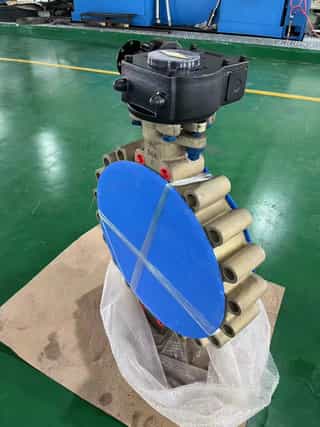
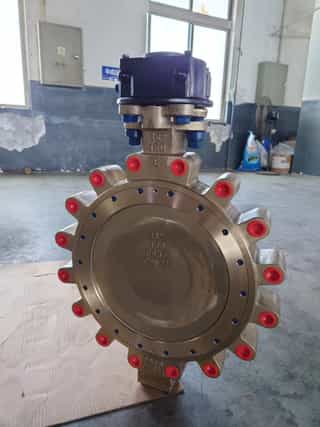
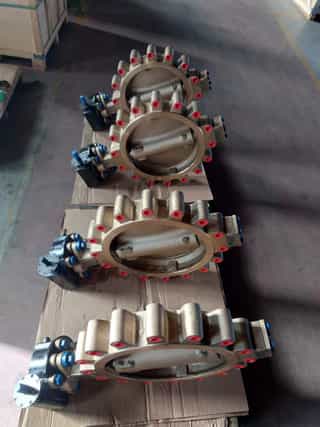
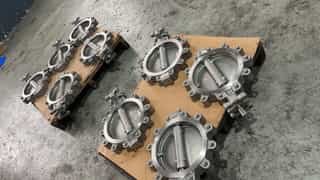
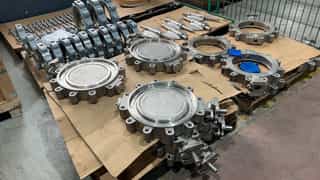
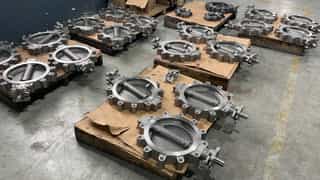
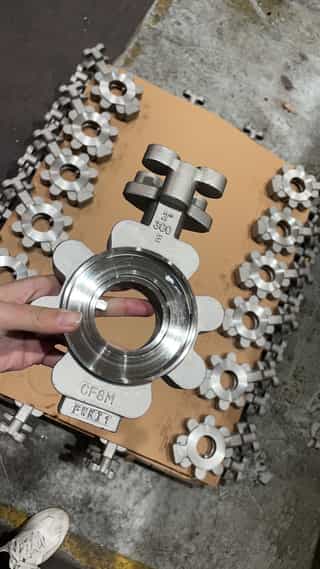

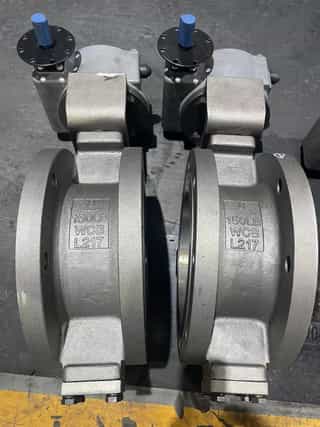
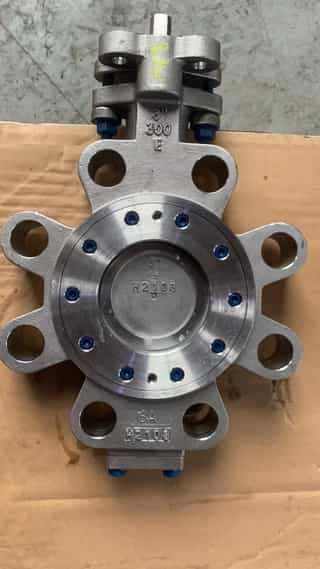
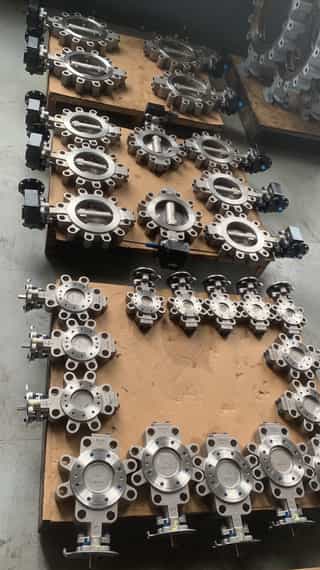
Butterfly Valve
In the realm of fluid control, the butterfly valve stands out as a versatile and efficient solution for regulating flow within pipelines. This comprehensive overview delves into the intricacies of butterfly valves, exploring their structure, industrial applications, usage instructions, failure analysis, and more.
Structure of Butterfly Valve
The butterfly valve derives its name from the wing-like disc that controls the flow of fluid through the valve. Let's delve into its key components:
Body
Similar to other types of valves, the body of the butterfly valve provides the housing for internal components and serves as the conduit for fluid flow.
Disc
The disc, resembling a butterfly's wings, rotates within the valve body to modulate the flow of fluid. Its streamlined design minimizes turbulence and pressure drop.
Seat
The valve seat forms a tight seal with the disc when closed, preventing leakage and ensuring efficient flow control.
Stem
Connecting the actuator to the disc, the stem facilitates the rotation of the disc to open or close the valve.
Actuator (Optional)
Some butterfly valves incorporate an actuator, such as pneumatic, electric, or hydraulic, to automate the valve operation for remote control and monitoring.
Industrial Applications
Butterfly valves find widespread use across various industries due to their versatility, reliability, and cost-effectiveness. Here are some primary applications:
Water Treatment
In water treatment plants, butterfly valves regulate the flow of treated water, raw water, and chemicals, facilitating efficient processing and distribution.
Chemical Processing
In chemical manufacturing facilities, butterfly valves handle corrosive fluids, acids, and alkalis, providing robust and dependable flow control in demanding environments.
Oil and Gas
Within the oil and gas industry, butterfly valves are used in pipelines, storage tanks, and refineries to control the flow of crude oil, natural gas, and petroleum products, enhancing operational efficiency and safety.
Food and Beverage
In food processing and beverage production, butterfly valves regulate the flow of ingredients, liquids, and gases, meeting stringent hygiene and quality standards.
Usage Instructions
Proper installation, operation, and maintenance are essential for maximizing the performance and lifespan of butterfly valves. Here are some key instructions:
Installation
- Ensure proper alignment and orientation of the valve to facilitate optimal flow direction and sealing.
- Tighten all connections securely to prevent leaks and ensure structural integrity.
Operation
- Use the appropriate actuator, if applicable, to control the valve's position and flow rate according to system requirements.
- Regularly monitor valve performance for any signs of leakage, corrosion, or abnormal operation.
Maintenance
- Conduct routine inspections to check for wear, corrosion, or damage to valve components.
- Lubricate moving parts, such as the stem and disc, to maintain smooth operation and prevent friction-induced wear.
Failure Analysis
Despite their durability, butterfly valves may experience failures due to various factors:
Corrosion
Exposure to corrosive fluids or environments can degrade valve materials over time, leading to leakage and reduced performance.
Seal Degradation
Prolonged exposure to high temperatures or aggressive chemicals can cause deterioration of the valve seat and seal, resulting in leakage and inefficiency.
Actuator Malfunction
Failure of the actuator, whether pneumatic, electric, or hydraulic, can lead to loss of control and improper valve operation.
Mechanical Wear
Continuous cycling and operation of the valve can cause wear on the disc, stem, and seat, affecting sealing and flow control.
Improper Installation
Incorrect alignment, inadequate support, or insufficient clearance can lead to binding, sticking, or uneven wear of valve components.
Frequently Asked Questions (FAQs)
Q1: How does a butterfly valve differ from a ball valve?
A1: Butterfly valves use a disc that rotates to control flow, while ball valves use a spherical ball with a hole to regulate flow. Butterfly valves are typically more compact and lighter than ball valves.
Q2: Are butterfly valves suitable for use with abrasive or slurry fluids?
A2: While butterfly valves can handle a wide range of fluids, including slurries and abrasive media, special considerations may be necessary to prevent erosion and wear of valve components.
Q3: Can butterfly valves be used for throttling or regulating flow?
A3: Yes, butterfly valves can be used for throttling applications, but they are generally better suited for on/off control rather than precise flow regulation.
Q4: What factors should be considered when selecting a butterfly valve?
A4: Key factors to consider include the type of fluid, temperature and pressure conditions, flow rate requirements, compatibility with system materials, and operational environment.
Q5: How can I prevent leakage in a butterfly valve?
A5: Proper installation, regular maintenance, and selecting the appropriate sealing materials are essential for preventing leakage in butterfly valves. Inspecting and replacing worn seals as needed can help maintain sealing integrity.
Conclusion
In conclusion, the butterfly valve emerges as a versatile and reliable solution for fluid control applications across various industries. Its simple yet effective design, coupled with ease of installation and maintenance, makes it a preferred choice for regulating flow in pipelines, HVAC systems, chemical plants, and more. By understanding the structure, applications, usage instructions, failure modes, and FAQs of butterfly valves, engineers and operators can leverage their capabilities to achieve optimal fluid control with efficiency and confidence.